Machine failures are a blight on industries the world over. While some are sudden and unexpected, the truth is that many of them can be prevented by proper maintenance.
The key is information, and when running a busy operation, info isn’t always easy to come by. That’s why setting up a custom maintenance report form can help you get the correct data on time and help to put a stop to preventable breakdowns in your department.
How To Use This Short Guide
Every workplace is different, which makes ‘custom’ the keyword here. This guide serves as a general roadmap to get the correct information in hand. You know your machines, and you’ll know if you require additional information.
Most workplaces will benefit from the fields included in this guide, so give it a read through and take a crack at setting up your maintenance report form. We’ll even include a handy template at the end, so you can grab and adapt it to your specific situation.
If you’d like to explore Mobile Forms and build your maintenance report in Appenate, this guide to mobile forms is a great place to get started.
Anonymous Information Is Useless
The first thing you’ll want to capture is who’s doing the job and the job number when applicable. You might also want to include a time field to get a general idea of how long each job takes.
This way, you’ll be able to see how busy your technicians are and who’s available to swing over to a machine failure when the need arises. You also might have questions about the job or even spot discrepancies and be forced to take disciplinary action. Adding identifying information saves you from running around for this.
At any rate, always be sure to include this most basic of information in your reports.
Safety First
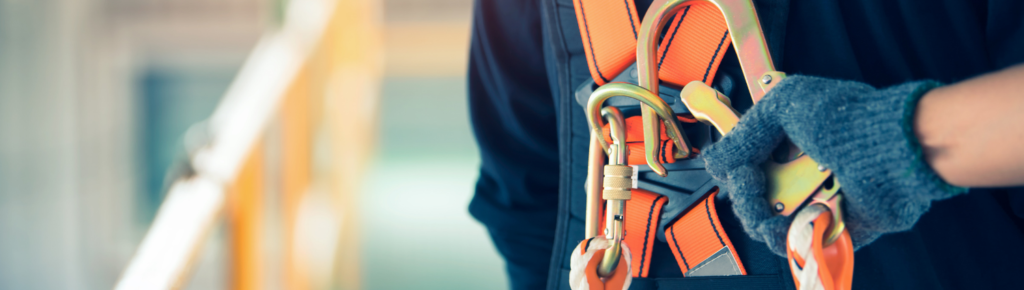
Before your technicians even touch the machines, they should perform their safety checks.
Here are some examples.
- Is the machine safely locked out? (operating station physically locked, power disconnected and physically locked, etc.)
- Is the work area clean and free of slipping, tripping and falling hazards?
- Is the correct personal protective equipment (PPE) in place and in good condition?
- Are the correct tools for the job present and accounted for?
These are just a few of many checks to include. If you’d like, you can be more specific about the PPE – for example, if a machine is on the first or second floor and near a drop, you can make the harness number and certificate mandatory to begin work on this machine.
Safety protocols can seem absurd at times, but it’s for a good reason most of the time. The truth is that lives are at stake in many work environments, and we must do all we can to prevent loss.
Machine & Maintenance Identification
All the information in the world will do you no good if you don’t know which machine it applies to. Similarly, it won’t help if all you have is a “machine was checked” checkbox. It’s wise to capture the machine identification number and outline the maintenance checks.
For example, you might want the technician to check and then top up the oil levels, note how much oil was consumed, check the bearings and moving parts, etc. – each item should be on its own line.
The two main reasons for this are new and seasoned employees. The former may not know all the checks necessary on a certain machine. Seasoned employees may submit to a level of comfort that compels them to skip certain checks (personally seen this happen).
So be sure to set the checks out properly so that accountability isn’t lost if something does go wrong.
Jobs Are Rarely Hitchless
With every preventative maintenance checkup, there WILL be subsequent steps to add. This will often just be the next checkup, but when required repairs get identified, technicians must note these down along with their level of urgency.
Leave enough room on your form for the technicians to add specifics to the found issue. The technician who found the problem might not be the one to repair it, so for that reason, no detail can be left out. The technician should add a comprehensive description and photos (if possible) to the maintenance report form.
From here, this information will go to the maintenance planner, who can then schedule the repair promptly.
The indication of urgency is essential, and we’re restating it here. It’ll make the Maintenance Planner’s life easier, and they can prioritise and dispatch their technicians with greater accuracy.
Always Capture Proof Of Work
In maintenance, photographs are priceless. We cannot stress this enough. Before-and-after pictures are great. Whether it’s just the oil level or a newly replaced bearing, these images can work wonders for data integrity and (by extension) insurance claims.
Photos of the clean workplace and in-tact PPE can also help to limit liability.
A digital platform works great for this – but more on that in the next section.
Whether you can add photos to your form or not, always leave room for the technician, machine operator and safety representative to add their signatures and the date.
This pretty much completes your maintenance report form. Now it’s time to take stock of what you have and put it to the test.
Print And Test The Form?
It’s time to print out that form and hand it to your technicians. Before you print, however, consider this…
A digital mobile app solution can cut your admin time by as much as 80%. What’s more, it can save all sorts of unexpected costs associated with paper, like printing, data capture, storage and even the fuel cost of transporting paper.
With Appenate, you can build out your form, word-for-word, using our drag and drop app builder. There is a learning curve, but we offer free training and support for life, so you won’t be left to ‘figure it out’ by yourself if you need help.
Note that there’s a flat learning curve on the technician’s side. They simply open the app on their phone, tap the form or app they need and fill in the information.
We have a handy return on investment calculator here, as well as the guide to all things mobile forms here (also linked above).
Whatever you decide, we hope that you’re at least one step closer to stopping preventable machine failures for good! 😉
Grab Your Template Here
You can find a Google Sheets Template here (add a copy to your drive to edit it).
If you’d like to try Appenate free and obligation-free, click here to sign up.