Being a Logistics Manager is no easy job. You’re a maestro of moving parts that are largely invisible to the naked eye. Keeping track of all these parts often feels like wading through dark waters. If we want to survive and evolve, we need agile systems in place.
Thankfully, modern-day software has our back. The right tools can give us what we need to achieve our desired operational efficiency.
This post will highlight eight ways software helps leaders in logistics. With booming customer expectations, technology is co-paving our way to success.
Let’s dive in.
1. Lack of Visibility Across the Supply Chain
Not too long ago, timely supply-chain updates were hard to come by. We had no choice but to depend on periodic reports and fragmented data. With no real-time insight, staying on top of things was nearly impossible.
Evolving software solutions have stepped in to save the day. We can now track the entire product life cycle from start to finish – in real time.
The most popular types of software for boosting supply chain visibility are…
Supply Chain Visibility Software
Also known as ‘track and trace’ solutions, this type of software tracks your products from raw to ready (to keep it short). These systems are typically capable of basic inventory management, data analysis, and ETA calculation.
Project44 and Overhaul are the ‘titans’ of supply chain visibility. They have features like geofencing and shipping trackers that simplify complex chains.
Supply Chain Management Software (SCMS)
While akin to Supply Chain Visibility software, this ‘sibling’ focuses more on general management. At its essence, it allows you to automate and optimise product flows.
Figure out your needs first, and then assess whether the solution fits before you spend a dime. Certain sub-industries may find some tools in this space ill-fitting to their needs.
One of the industry favourites for mid-market businesses is Anaplan. This software has scored high on scenario modelling, forecasting, and nifty dashboarding.
2. Subpar Demand Management Processes
The cornerstone of effective demand planning is predictive analysis.
Before full-scale automation, statisticians worked overtime to make sense of it all. Decoding data manually takes forever, and with little time at their disposal, managers were often at a strategic disadvantage.
Demand management software tilted the scale with powerful algorithms to restore that advantage. These intelligent solutions create ‘what if’ scenarios to help us predict various outcomes. We link the software to our customer database, it tends to the chaos in the middle, and we get to draw actionable insights on our end.
Anaplan takes the trophy here, too (according to Trust Radius). With their proprietary Hyperblock™ technology, Anaplan empowers you to make data-driven decisions.
3. Manual Effort and Reliance on Paperwork
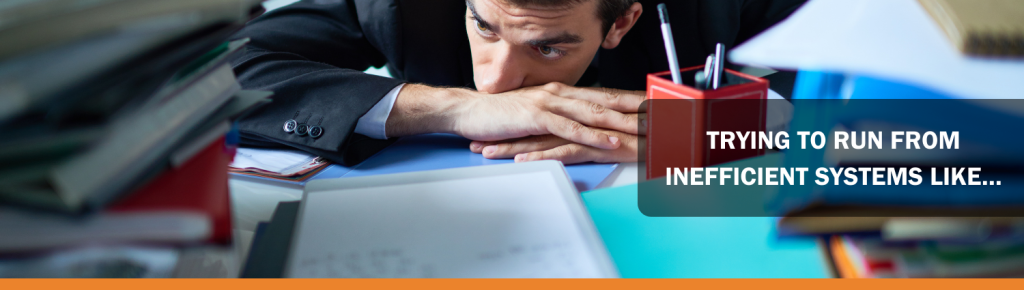
The downsides of physical paperwork are well-known. If you’ll excuse a brief metaphor, It’s like going to the Autobahn but in a Peel P50. Why set yourself up for disappointment when better systems are readily available?
With digital data management, we can optimise and save costs on administration.
If you’re not up to date on the digital transformation front, this is the best place to start.
There are many data management systems available in the market today. To choose the best fit for your business, make sure you select a system with these qualities;
- Mobile Data Capturing – for on-the-go write-ups on stock, staff, and incidents.
- High-level integration Capacity – to easily connect to your local databases.
- Flexibility – cookie-cutter solutions are pricey and often limited. Every operation is unique and usually requires an agile solution to match.
- Scalability – watch out for data storage caps that may break the bank to remove. Make sure your chosen solution can handle your data requirements from the very start.
- Customer Support – prevent downtime by picking solutions with well-rated, free support.
- Data Protection – double-check the data privacy policy of your provider before you subscribe.
Ever heard of Appenate? You might’ve noticed that we’re the owners of this site and wondered how we fit into logistics. It’s pretty simple – our mobile app builders adhere to all of the above. We’ve been helping managers switch over to digital systems for over 10 years. And our unmatched customer support is just one aspect of what sets us apart.
Here’s an example of how one of our certified consultants helped a fuel distribution company kick paper-based admin for their drivers.
Visit our homepage if you’d like to learn more about our offering. That’s the pitch done; back to the blog post. 😉
4. Inefficient Transportation Management
Picture this – you send your driver on his way to complete the day’s orders. He ventures off with nothing but his smartphone – yet you don’t fret like you used to. His phone will pick the best route so he can arrive on time, and you can track his progress every step of the way.
Transportation management systems have been helping managers to keep their customer ratings high.
Using cloud-based data, a suite of integrations, and real-time alerts, these solutions help streamline the following.
- Route Optimization -selects the best routes based on traffic updates and customer locations.
- Load Consolidation – gets the most out of the space we have available.
- Real-Time Tracking – paints a visual picture with advanced geo-locating.
- Carrier Selection – using predefined criteria, the best carriers are auto-calculated. Some software even enables you to communicate with your carrier directly.
- Exception Management – allows managers to preconfigure solutions to various ‘unforeseen’ events.
5. Complex Warehouse Management
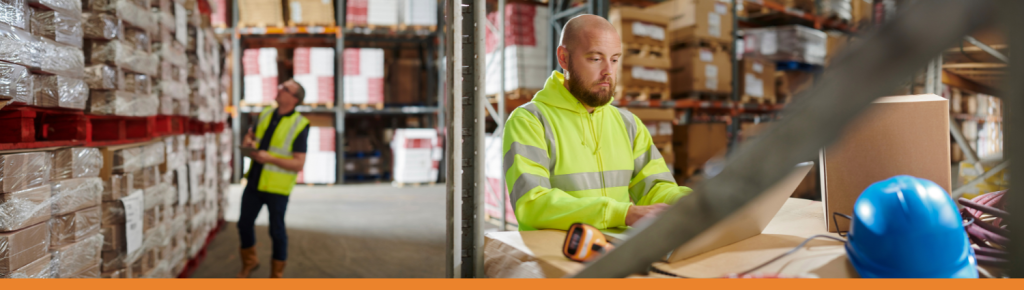
With many moving parts – the order of things really do matter.
Warehouse management software provides us with intelligent task sequencing. They help managers to plan ahead and find the best order in which to operate. Voice-picking systems can deliver verbal instructions to workers, helping them stay on track. These mobile systems can integrate with IoT sensors, making full-scale monitoring a breeze.
Many large warehouses are already equipped with a combination of these technologies. As advanced solutions become more affordable, smaller players will jump on board too.
6. Spotty Compliance
Compliance – a constant and formidable challenge. Thankfully, the tools to combat this headache grow – almost literally – by the day.
If we’re talking safety compliance, it’s probably best to get an industry expert to lead your digitalisation charge in this area. One of our consultants used Appenate to help her clients attain ISO45001 certification. Read the story here.
In this area of transformation, paper is a real pain. Digital reports, on the other hand, are easily managed, shared, and stored on cloud systems.
Come audit time, you’ll be pre-prepared and won’t have to dig through mountains of paper in the back office.
7. Inaccurate Inventory Reports
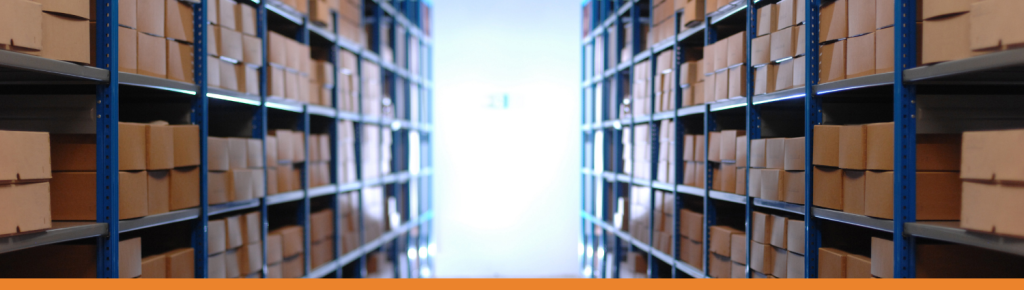
Inventory Management has changed for the better. Real-time alerts notify us when we hit specific targets (like reorder points) and help make our jobs more manageable. We no longer need to constantly keep an eye on physical stock levels. Once an alert drops, we just jump in and place the necessary orders.
The use of something called ‘Computer Vision’ has also gained prominence in larger warehouses. These powerful machine-learning technologies can take stock tracking and counting off our hands entirely. They’re also getting exceptionally good at flagging anomalies.
On the more affordable end, mobile apps ensure the swift and secure collection of data by workers on our warehouse floors.
If you’re interested, we covered the topic of ‘accurate inventory reporting’ here.
8. Broken Communication & Tardy Collaboration
With a centralised system, every key player can keep their eyes on the latest and most vital updates.
There are two main ways that software has revolutionised the way we stay connected.
Worker & Team Collaboration:
Cloud-based task management allows our team members to work together asynchronously. With mobile integration, workers can stay updated and transparent wherever they go.
When you invest in offline-capable solutions, your teams will be able to work anywhere—a no-brainer for teams out on the road.
GPS tracking further bolsters the visibility of your entire team. Having a moving map in front of you can help you track progress and liaise with external parties as needed.
Supplier Communication:
One helpful feature of quality Transportation software is its ‘supplier portals’. This allows vendors to receive essential updates within moments. Some suppliers even give vendors direct access to their databases, further streamlining the logistics workflow.
We’re able to form living systems of data that we can actually use in the modern era, severing our reliance on paper-based systems.
Technology Is Still Evolving
It’s incredible to see the innovations in tech working alongside our growing ambitions. With the right tools, we can bear the fruits of next-gen efficiency.
And it doesn’t stop there. Technology still evolves every day – it’s only a matter of time before sprawling AI systems become readily available for most of the mundane tasks that humans simply don’t like. We’ll keep a keen eye on developments – and we suggest you do, too.
In case this is all a little overwhelming, here’s a simple step in the right direction.