Regulations are tightening, penalty costs are climbing & employee happiness is more important than ever – the way it should be. Yet, shouldering all that weight as a project owner or site manager can be overwhelming. That’s what inspired us to write this piece. There are things you can do to make the process less daunting. Getting on-site safety right from the get-go will save you a boatload of hassles.
In this post, we’ll explore the basics of internal site safety inspections, offer 5 tips to amp up the effectiveness of your inspections, and end with a bunch of resources on legislation for further reading.
Thank you for taking safety seriously; let’s get started.
Why You Should Never Skip A Safety Inspection
Every contractor aspires to complete their project without a host of unfortunate injuries, delays, or costly fines. That’s where site safety inspections can, quite literally, jump in to save the day.
In the United States, one worker loses their life to an on-the-job accident every 101 minutes ( Bureau Of Labor Statistics, USA, 2021 report.) While life lost is undoubtedly the worst possible outcome of negligent safety practices – penalty costs, lawsuits, project delays & a damaged reputation can all work their way into the consequences.
Hence, inspections are performed periodically to keep risks from materialising. It involves the infamous ‘checklist’ to document the conditions under which you execute a project.
Site safety inspections are best carried out daily. Once a week, where there is less predicted risk. The frequency and scope of safety inspections are decided before construction begins and stipulated in the ‘project safety plan’.
What Goes Into An Internal On-site Safety Inspection?

The scope of your on-site safety plan depends directly on the nature and complexity of your project. The higher the risk, the more extensive your lists will be.
A typical safety inspection will entail the assessment of…
The Worker Environment
No matter the size of your site, the risk of an incident looms around every corner. You can’t leave this to “common sense”. The more extensive your checklist, the better.
Complete environment inspections will include checking things like:
- Buildings & structures
- Atmospheric conditions
- Storage facilities
- Electrical power components
- Chemical storage
- Structural openings
- Personnel supporting equipment
- Overall facility hygiene
Personal Protective Equipment
Protective gear should always function optimally to minimise the risk of employee harm. Regular PPE inspections should be performed to check the gear’s quality and ensure that no wear & tear has occurred.
The typical inspection usually involves the assessment of gloves, helmets, eyewear & footwear.
For a comprehensive take on a PPE inspection, check out this publication by OSHA.
Equiment & Machinery
Where man and machine meet, risks abound. From entanglement to contact with live, open wires – horrors can ensue when you don’t regularly check your equipment.
As a rule, you should educate your workers on properly handling equipment, and instruction manuals should be readily available for all to inspect at any moment.
The usual pre-operating inspection will double-check things like machine shields & guards, power transmission guards, fixed location machine anchors, etc.
For a highly-visual guide & a bunch of general templates for easy printing (although we typically don’t encourage the use of paper), check out this post by HSSE.
Emergency Equipment
The last thing you want in an emergency is an idle & panicked team that doesn’t know where to find (or how to use) basic emergency response equipment.
Your team should be trained in emergency response, know all the safety protocols by heart, and have easy access to the tools that can diffuse a dangerous situation.
Fire extinguishers, first-aid kits, a visible list of emergency contacts & a working alarm are the bare minimum you’ll need.
5 Tips For Performing More Thorough On-site Safety Inspections
“Thorough” is the keyword here. You want to bolster your organization against sudden liability every step of the way. Having rigorous safety measures can, unfortunately, take a lot of consistent effort.
Luckily, there are always techniques & systems you can implement to make it easier.
Here are five things that many companies are doing to lighten the weight of routine safety practices. Things that might change the game for you too!
1. Standardise The Process
Plan appropriately at the start of every project.
Your on-site safety plan should include things like:
- Hazard identification sheets
- Training plan & schedule
- Inspection dates & area diagrams
- Checklists to use
- Emergency response protocols
- Details of the employees assigned
The value of standardisation is that everyone gets to be on the same page & safety reports can stay consistent – a big help when third-party inspectors rock up on site. Always be open to suggestions from professionals, however.
2. Educate, Assign Responsibility & Encourage Accountability
To avoid a bad case of the bystander effect, ensure that every worker on site has a role to play in your safety protocols. Employees should know the roles of their team members & safety drills should be carried out occasionally to cement that information into memory.
The best thing to do in a high-risk environment is to encourage a safety culture in your workers. HR Shelf released an insightful piece on motivating employees to establish a safety-first culture – give it a read.
3. Incorporate Visual Data
Whether you’re reporting on machine defects, working equipment or the aftermath of an incident – photographic evidence can carry you in the face of insurance claims, compliance & establishing liability, to name a few.
The best way to capture imagery on the job is by using construction management software that locally integrates with your mobile device.
4. Utilise Real-time Data
Time is of the essence here & immediate feedback is paramount when dealing with risks of any kind. To avoid extensive project delays & potential harm to your people or machines, we advise you to have a centralised system for instantly sharing reports & flagging risks.
Real-time data enables faster & more effective corrective action when something goes wrong.
5. Digitise Your Reports
Cramping an office with three years worth of paper reports is bound to toss some disorganisation into the process. Lost or misplaced papers can take hours, if not days, to recover or refile.
Having to courier every single report to authorities and back for an approval signature also wastes time you could spend doing other important tasks. It’s about time we leave the ho-drum tasks to computers – they’re better at handling the details anyway.
There are a myriad of benefits you can unlock by just going paperless and hopping onto an offline-capable, cloud-based system instead.
One massive win you’ll experience with project management software is that it dramatically reduces your time on admin tasks. It’ll also transform your ability to keep all the documents visible & easily accessible for the rest of your team.
Appenate, our mobile app-building software, is perfect for all of the above, allowing the creation of unlimited mobile apps without ever touching code. Our software scales with your business & allows you to flexibly drag and drop all the components you need on your forms.
All your data is captured on secure cloud storage and is readily accessible whenever you need it. Plus, the apps even work offline.
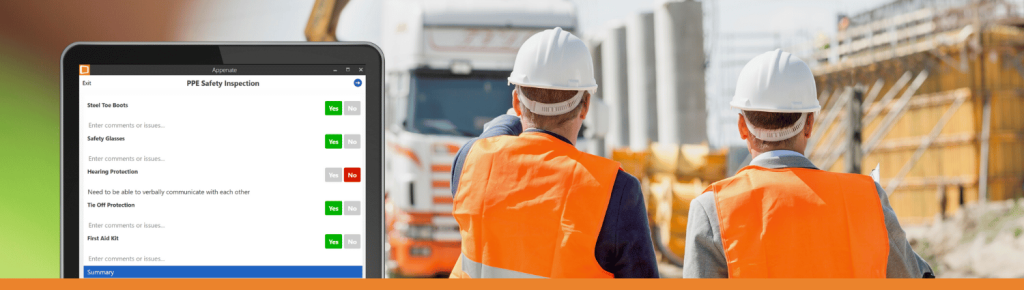
We have over 20 construction-specific app examples ready to go. By signing up to Appenate’s free trial, you can easily install any one of these for a quick start.
To name a few…
- Daily Report
- Accident Report
- PPE Inspection Checklist
- Timesheet
- Invoice
- Project Completion Checklist
- Pre-start Record
- Material Order Form
- Work Activity Safety Permit (WASP)
- Safe Work Method Statement (SWMS)
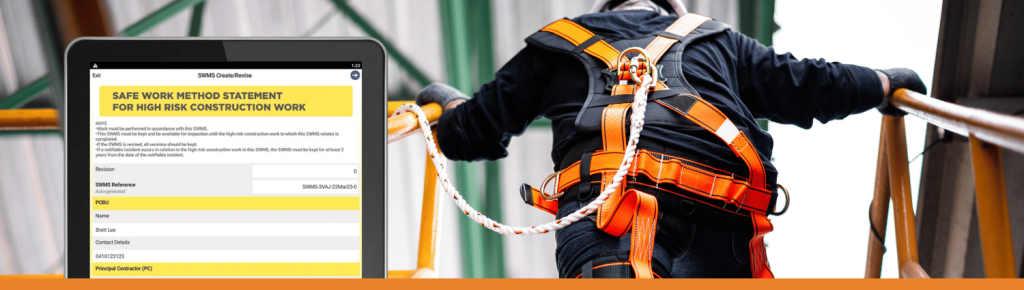
Notes On Legislation & Regulatory Requirements
As always, legislation & regulatory standards are set out by local governing bodies and are specific to location and industry. Always consult a professional when possible before making big safety decisions.
Here are a few location-specific resources for learning about the legal side of safety inspections for various industries.
For readers in the USA:
- OSHA for all things on Occupational Health & Safety. They enforce standards, offer training & provide assistance to meet the official standards.
- NHTSA works toward safer roads with their vehicle safety standards, investigations & recalls.
- FAA, with their mission to provide the safest aerospace system in the world.
- EPA serves the protection of the environment & human health.
- NRC is currently responsible for promoting the safe use of nuclear materials & facilities.
- MSHA oversees health & safety for the mining industry.
- PHMSA is the regulatory body for the transportation of hazardous materials.
For readers in the UK:
- HSE – The OSHA of the UK, enforcing Health & Safety standards in the workplace.
- DVSA – regulating the safety standards of vehicles, conducting driver tests & issuing licenses.
- CAA oversees all aspects of civil aviation regulation.
- ONR, in charge of nuclear regulation.
- MCA regulates safety in the maritime industry, dealing with ships, ports & installation regulations.
- HSENI is responsible for enforcing the Health & Safety standards in Northern Ireland.
- SEPA tends to the health of the environment & the people in Scottland.
For readers in Australia:
- SWA – regulating & enforcing Health & Safety laws.
- ATSB is Australia’s national transport safety investigator.
- CASA – regulating aviation safety.
- AMSA, from protecting the marine environment against pollution to aviation & maritime rescue services.
- NHVR is a ‘heavy vehicle’ regulator based in Brisbane.
- ABCB – ensuring the safe & sustainable construction of buildings & plumbing installations.
- APVMA – the regulator of agricultural and veterinary chemical products.
A Safer Work Environment Starts With You
We hope this piece provided you with something you can put to good use. Inspections are the lifeline of Health & Safety, and it deserves the extra thought you’re giving it.
We’re invested in this topic because so many of our clients use us to optimise their safety processes, and we’re excited to play a part where it matters most.
Read our case study with Geeks Are Good (an Appenate Consulting Partner) to see how our platform helped a business in the chemical industry to bump up their incident reporting rates.
That’s it for now. All the best to your safety efforts going forward.